Phaseshift Technologies, an AI Materials Company, Creates Alloys for Energy, Aerospace, Mining and Automotive applications.
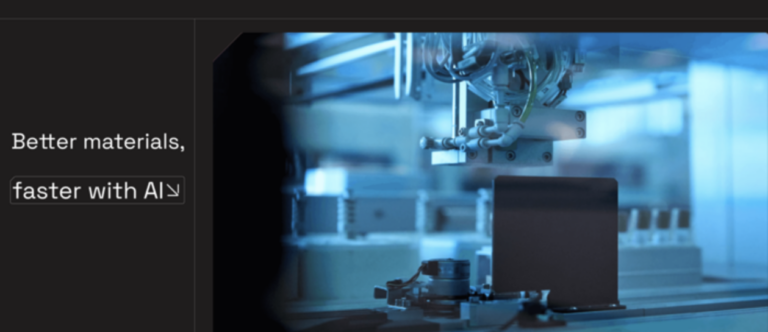
From the Stone Age, Bronze Age to Iron Age, the progress of human civilization is also a history of material development from a certain perspective. Nowadays, materials can still be seen everywhere around us, from the towering skyscrapers to the tiny but powerful smartphone chips. However, with the development of science and technology, the requirements for materials in various industries have become more stringent.Many industries are constrained by the inherent properties of existing materials, making it difficult to make further breakthroughs.
For example, the design of smartphones has basically reached the optimal level in terms of strength and weight. That is to say, due to the current development status of related materials such as glass, aluminum alloy, and batteries, it is difficult to reduce the weight of mobile phones by leaps and bounds. Lightweight materials such as plastics are also limited in strength - they are less scratch-resistant and durable.
Developing a new material that combines high strength with low weight is not easy.The development of new materials is not only costly and time-consuming, but also carries extremely high risks.Typically, the R&D investment for a new material can reach $100 million and take at least 10 years to achieve financial breakeven.
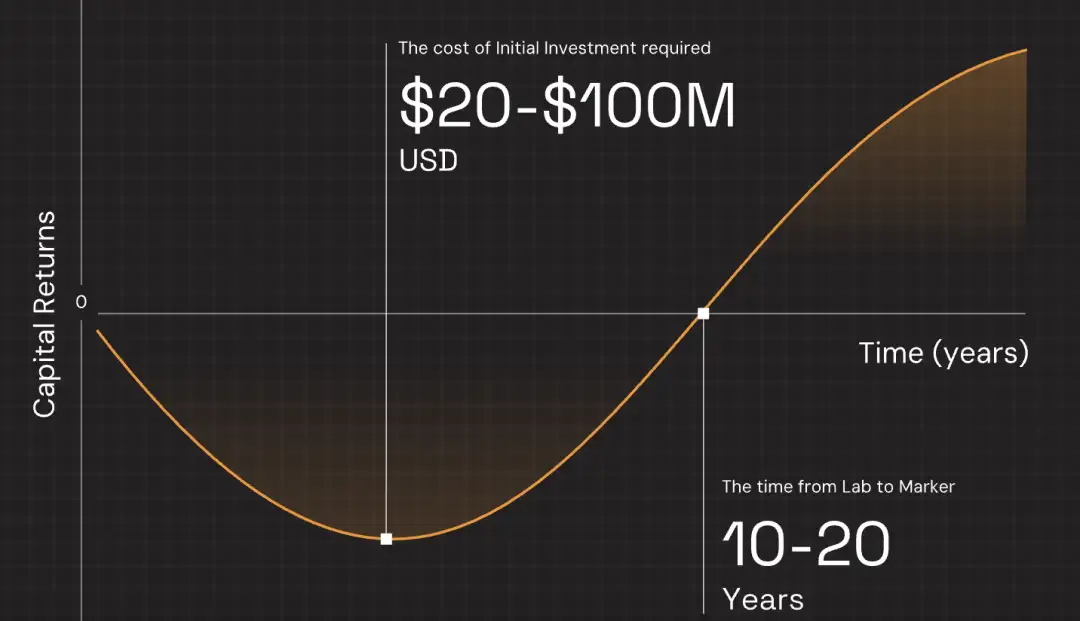
For a long time, only strategic industries with sufficient funds such as aerospace and defense have the ability to develop proprietary materials, while fields such as mining, energy, consumer electronics and manufacturing still face many challenges in material development. Therefore, many companies prefer to use existing materials, such as relying on alloys developed half a century ago.In this case, some compromises have to be made:
* Are more expensive material costs passed on to consumers?
* Is it acceptable to accept a critical component, but with a shorter lifespan?
* Are higher maintenance costs acceptable to compensate for the lack of material performance?
* Are some innovative designs being abandoned in favor of the physical properties of traditional materials?
* Will they continue to rely on imported supply chains and endure the uncertainty brought about by scarce or expensive raw materials?
Canadian company Phaseshift Technologies has provided a solution to the above dilemma.
In 2019, Phaseshift Technologies, an advanced materials company, was officially established in Canada.Committed to developing next-generation alloys and composites using AI technology and multi-scale simulation.Its Rapid Alloy Design (RAD™) platform, based on MatterMind™ (AI-driven alloy design) and Cascade™ (integrated multi-scale simulation), can develop customized alloys for specific needs and scenarios in a variety of industries.
According to Phaseshift’s official website,The method speeds up material development by 100 times compared to traditional methods while reducing costs.In addition, the alloys designed by it can be widely used in aerospace, automobile, energy, defense, mining and advanced manufacturing industries.
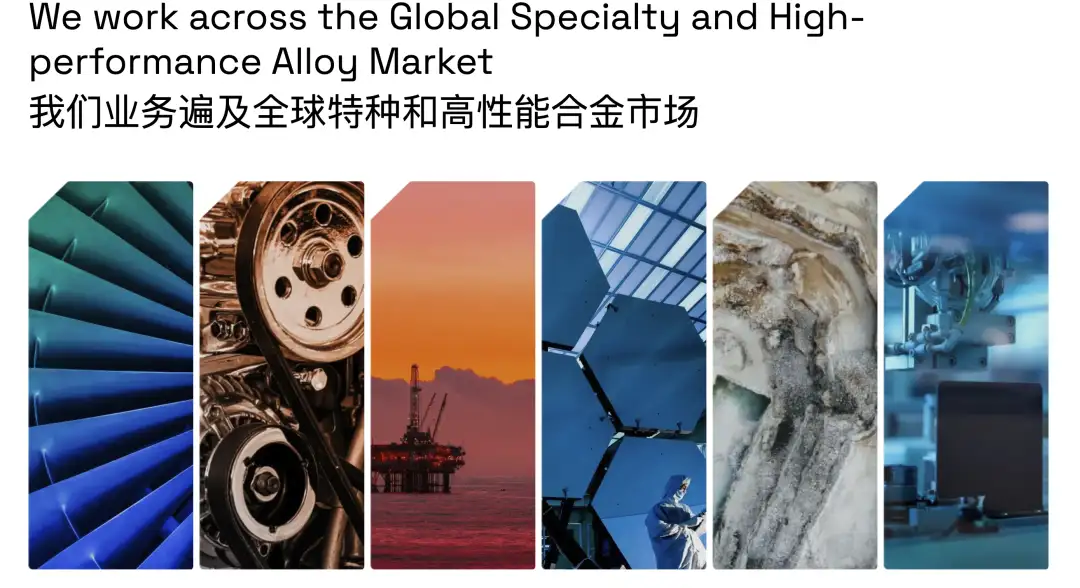
* Aerospace: Next generation alloys enable improved performance, lightweighting, and increased fuel efficiency while meeting safety standards.
* Automotive: Creating lighter, stronger alloys that improve fuel efficiency, safety and enable innovative vehicle designs.
* Energy: Custom alloys can withstand extreme conditions, improve equipment durability and efficiency, and reduce maintenance costs.
* Defense: Advanced alloys provide superior performance and durability, ensuring reliability in critical missions.
* Mining: Durable alloys can withstand harsh environments, extend the life of equipment, and increase mining productivity.
* Advanced Manufacturing: Customized alloys can improve product performance, durability and design flexibility, driving innovation in manufacturing processes.
Currently, Phaseshift has completed a $3 million seed round of financing, led by Innospark Ventures, with participation from Draper Associates and First Star Ventures, and additional support from angel investor Hustle Fund Angel Squad. This funding will enable Phaseshift to accelerate the development and commercialization of new materials.
Fazal Mahmood, co-founder and CEO of Phaseshift, said:When the development of certain industries is limited by the inherent properties of existing materials, material-level innovation becomes critical.Our AI platform enables rapid development of specialized materials to solve overlooked real-world industrial challenges. By delivering more durable, efficient, and sustainable materials, we are helping industries reduce waste, lower maintenance costs, and push the limits of engineering and manufacturing."
AI + multi-scale simulation to develop next-generation alloy materials
Designing new materials is like mixing a complex recipe with a large number of ingredients. In the past, scientists used trial and error to find the best recipe, just like chefs, by repeatedly adjusting the proportions of the ingredients and observing the effect of each change on the final "dish".
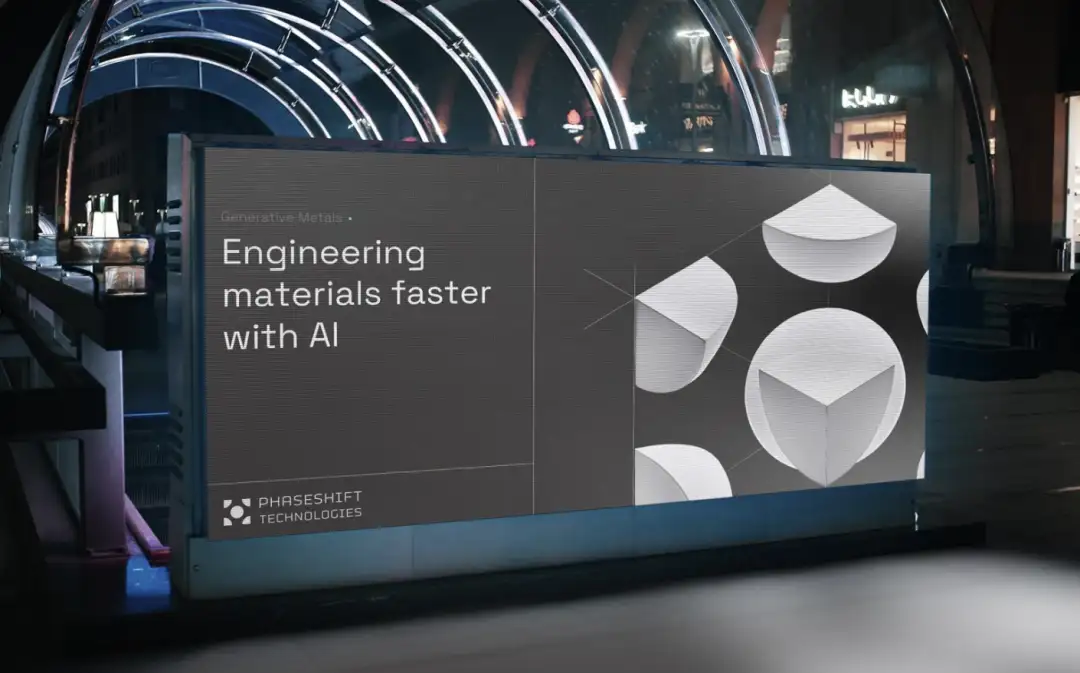
Today, Phaseshift lets artificial intelligence play the role of the “chef”. It not only knows all possible combinations of “raw materials”, but also predicts how each ingredient affects the overall “flavor” of the material, thereby finding a potential “perfect recipe”. Furthermore, advanced computational models can also simulate and evaluate these recipes. In this way, researchers can quickly explore countless combinations of alloy “ingredients” and “cooking methods” without having to conduct endless real-world experiments.
Specifically, as shown in the figure below,In Phaseshift's platform, new alloy development goes through five steps.First, the user provides the alloy purpose, and the company determines the design requirements; second, MatterMind™ uses AI methods to produce new optimized alloy compositions; third, Cascade™ evaluates alloy performance through multi-scale simulations such as nano, micro, and macro, and updates the AI model, repeating the above steps until the design requirements are met. Fourth, cooperate with laboratories to conduct realistic evaluation of materials using industry-specific qualification standards. Fifth, use customized alloys to gain market competitive advantages.
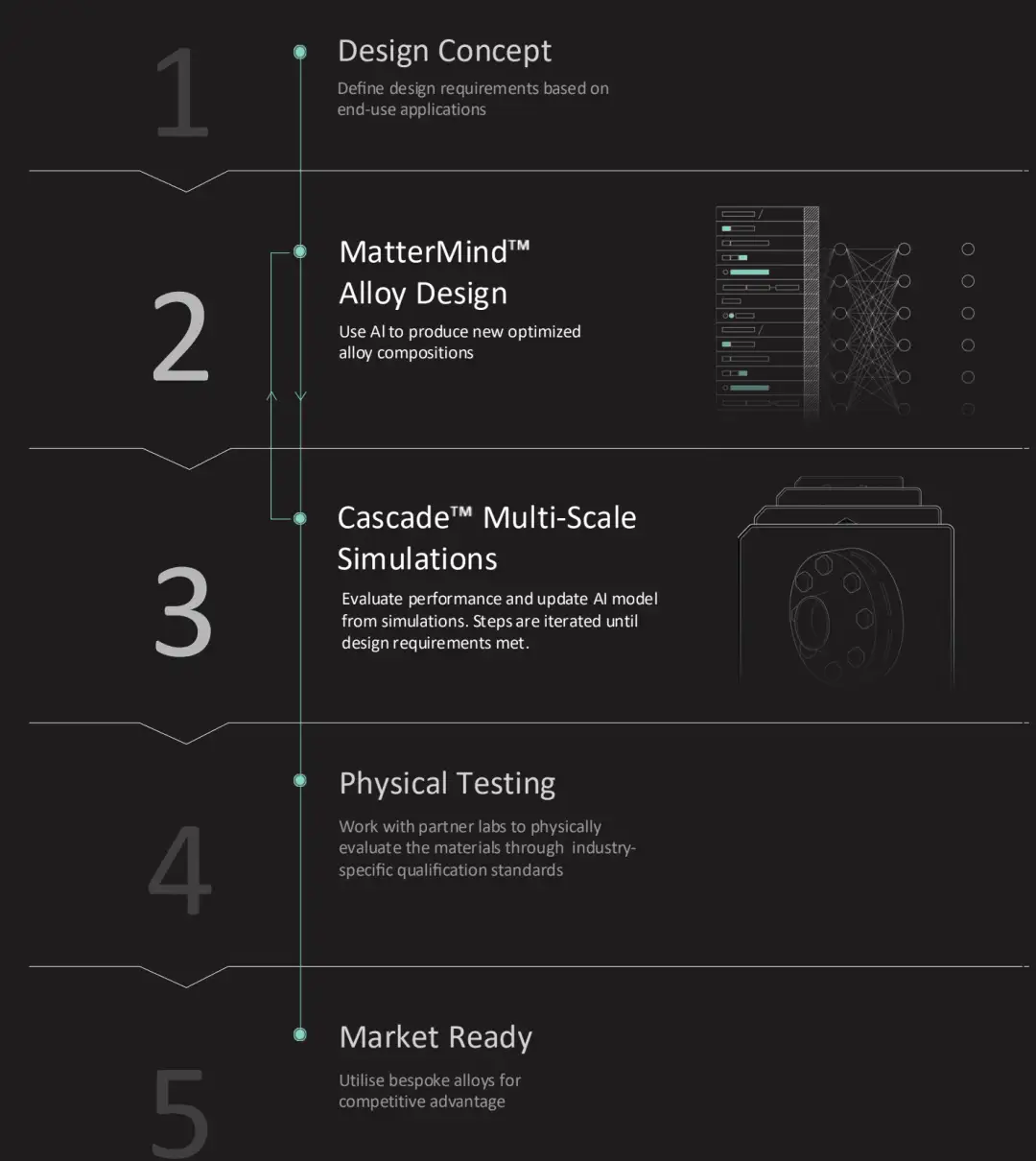
In order to achieve the above technological breakthroughs, Phaseshift has brought together a group of experts in the fields of AI and materials science.Such as Dr. Osazee Ero, a machine learning researcher, and Dr. Zhen Li, a computational materials engineer. Dr. Osazee Ero has more than 8 years of experience in machine learning research and is good at designing advanced AI algorithms, especially in the manufacturing field. Dr. Zhen Li has extensive knowledge in materials science, FEM simulation, and advanced modeling techniques, and has 8 years of experience in numerical simulation of metallurgical processes. He believes that "modeling and simulation are not only tools for understanding materials, but also the key to engineering innovation."
MatterMind™: Proprietary data-driven AI model to design the “perfect alloy”
The key to training an excellent AI model is to have a batch of high-quality specific data. However, data in the field of materials science is often scattered and of varying standards. Many experimental data exist in academic papers, corporate laboratories, or proprietary databases, and public data is extremely limited.
To solve this problem,Phaseshift uses a combination of experiments and simulations to autonomously generate high-quality datasets.This approach ensures the consistency and reliability of data across contexts, providing a solid foundation for the MatterMind™ platform.
MatterMind™ combines machine learning with physics-based modeling.First, by training on proprietary alloy datasets (existing and simulated data), MatterMind™ can quickly analyze a vast space of alloy compositions, predict optimal alloy formulas, and reveal complex nonlinear relationships between elements, processing conditions, microstructures, and material properties, which often go beyond human intuition and cannot even be directly expressed in mathematical formulas. Second, known scientific knowledge in materials science, physics, and chemistry is also integrated into the model, giving it stronger predictive power and identifying new alloy compositions that may meet target properties.
In addition, MatterMind™ is paired with advanced multi-objective optimization algorithms.Find the best balance between multiple properties. For example, an alloy needs to be lightweight, high-strength, minimal ductility, chloride corrosion resistance, weldability, etc. Traditional methods are difficult to optimize such a complex combination of properties, while AI models can use patterns learned from data to balance multiple design goals, thereby developing high-performance materials that meet specific industrial needs.
final,MatterMind™ can design an optimized set of potential alloy compositions without having to conduct extensive real-world experiments.It is then sent to the Cascade™ platform for simulation and evaluation, and MatterMind™ is continuously optimized and iterated based on the simulation results.
Cascade™: Multi-scale simulation to fully evaluate potential alloys in a virtual environment
Cascade™ can perform multi-scale simulations at nanoscale, microscale, mesoscale, and macroscale.This allows accurate modeling of how microstructural features (such as grain size, phase distribution, and defects) affect the overall performance of an alloy, allowing for a preliminary assessment of potential alloys and ensuring that the most promising alloys enter the manufacturing stage.
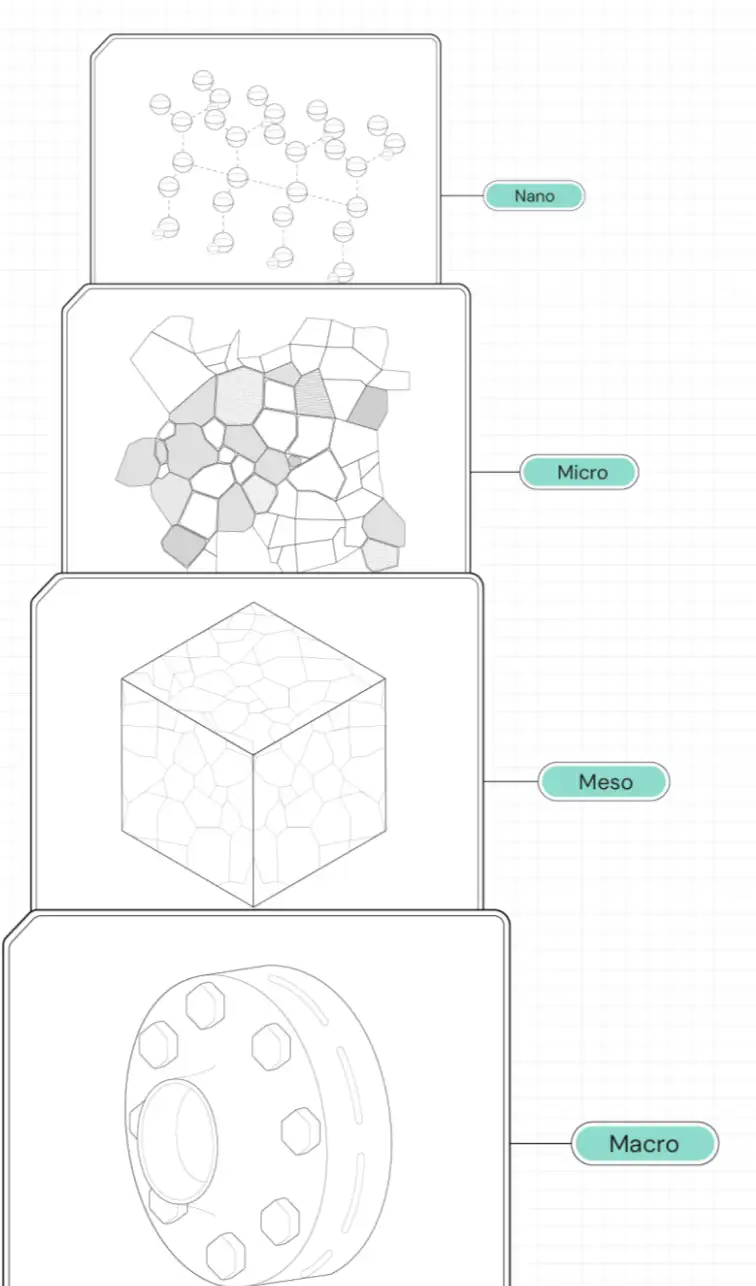
* Nanoscale: Using density functional theory (DFT) to predict the interactions between atoms of different alloying elements.
* Microscale: simulate microstructural evolution and predict grain structure and grain boundary behavior.
* Mesoscale: models the response of materials to external conditions.
* Macroscale: Simulating the mechanical properties of materials and their performance in different manufacturing processes (e.g. casting, additive manufacturing).
Through these simulations, hundreds or even thousands of potential alloys can be quickly evaluated in a virtual environment.And compare it with the user's design requirements. There is no need to manufacture physical samples or conduct repeated tests in the laboratory. This virtual evaluation method is cheaper and faster, and can accurately match the required material properties, thereby improving the success rate of R&D.
Customize multi-target property materials according to user needs and develop suitable alloys for 3D printing
According to Phaseshift officials,This approach can be used to develop suitable materials for additive manufacturing (3D printing) processes.
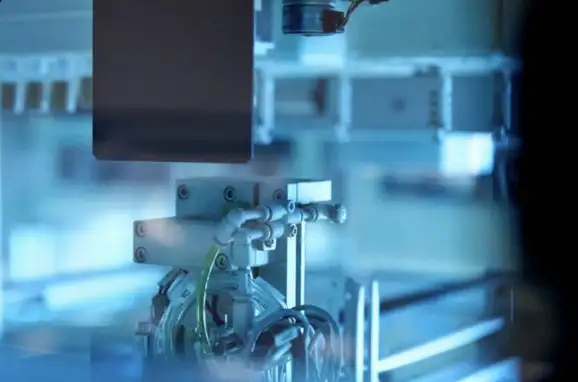
Additive manufacturing (3D printing) mainly builds three-dimensional objects by stacking raw materials layer by layer. At present, metal parts made by metal additive manufacturing technology have been successfully used in aerospace, medical equipment, automobile manufacturing and other fields. However, due to the adaptability of materials, the development of this process is still limited - the types of alloys that can be used for 3D printing are limited, which affects the wide application of the process and the performance of the final parts.
For example, the most common metal 3D printing process, laser powder bed fusion (LPBF), is only applicable to titanium, copper, and nickel alloys, and is prone to shrinkage and uneven melting during the manufacturing process. Although multi-laser LPBF improves production efficiency, it also increases the risk of material overheating. Other metal additive manufacturing processes, such as selective laser sintering (SLS) and electron beam melting (EBM), are also subject to the properties of the material itself and cannot meet multi-target requirements, such as thermal expansion, melting temperature, and part density.
Phaseshift has a custom R&D process specifically designed to optimize alloys for AM, modeling materials with different composition ratios and focusing on analyzing their performance in an AM environment to ensure optimal suitability.
“Whether it’s enhancing the strength of aerospace components, improving the thermal conductivity of automotive systems, enhancing the corrosion resistance of energy infrastructure, or making medical devices biocompatible,We can all provide custom alloys for more sustainable material solutions”, Phaseshift said.
Materials science is moving towards a more efficient and intelligent era
Cheng Xuan, a professor at the School of Materials Science and Engineering at Xiamen University in China, once pointed out that "the future of computational materials science will depend on the development of artificial intelligence. We should pay special attention to how AI can be integrated into material design and screening, and how to accurately design material structures based on target functions."
Nowadays, the application of AI in the field of materials science has gradually been implemented. From customized medical implants and smart prostheses to the development of new heat-resistant materials, advanced catalysts and degradable plastics, AI is accelerating product innovation in various industries.More and more technology companies are also aware of the huge potential of AI in materials development.
For example, Meta once launched the OMat24 dataset.The dataset contains more than 110 million structural density functional theory (DFT) calculations, focusing on the diversity of structure and composition, making it one of the largest public datasets in this field. Based on OMat24, Meta also released the EquiformerV2 model, which can accurately predict the ground state stability and formation energy of materials, and achieved the best performance on the Matbench Discovery leaderboard.
* OMat24 dataset download address:
In addition, Google DeepMind is also exploring the application of AI in material development.Its deep learning model GNoME announced the discovery of 2.2 million new inorganic material crystal structures, of which 380,000 are stable, making them the most likely potential new materials to be synthesized experimentally and put into use, greatly promoting the progress of materials research.
Microsoft launches MatterGen, a generative AI model for material reverse design.Ability to design new material structures directly according to specific needs. For example, when designing multi-property magnetic materials, the model can propose structures with high magnetic density and low supply-chain risk chemical composition. In addition, MatterGen is equipped with multiple adjustable modules that can be fine-tuned according to constraints such as chemical properties, symmetry and material characteristics to generate materials that meet specific magnetic, electronic or mechanical properties.
HyperAI has launched a tutorial "MatterGen Inorganic Material Design Model Demo" on its official website. The tutorial address is:
In summary, these companies demonstrate different entry points of AI in the field of materials chemistry, and also mark the new technological leap from large-scale discovery of materials to "on-demand design". With the continuous evolution of AI models, materials science is moving towards a more efficient and intelligent era.
References:
1.https://phaseshift.ai/
2.https://blog.csdn.net/a13981820402/article/details/140632362
3.https://www.sohu.com/a/140409967_488176
4.https://www.ccf.org.cn/YOCSEF/Branc