AI Quality Inspectors Are Employed in Fujitsu Factories, With Inspection Efficiency Increased by 25% Compared to Manual Inspection
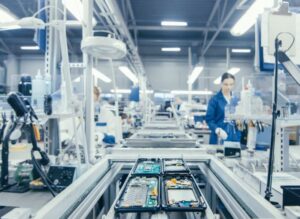
Fujitsu, Japan's leading IT manufacturer, recently announced that it has developed AI technology for detecting abnormalities in product appearance, thereby saving labor costs, material costs, etc., as well as reputation loss and costs related to returns/recalls. The "unmanned factory" has arrived.
Last November, Apple began to recall AirPods Pro worldwide. The reason was that AirPods Pro manufactured before October 2020 may emit popping or static noise, which may increase in noisy environments, during exercise, or during calls.
Unexpectedly, just one month after this incident, in December 2020, Apple launched a new round of recall plan targeting the previous iPhone 11 screen touch failure problem.

The repeated recalls of defective products have not only damaged Apple’s reputation, but also caused it to lose the trust of consumers to a certain extent.
Therefore, in addition to product performance indicators, quality control is also crucial for enterprises.
As people's consumption level improves, the demand for electronic products increases, and the pressure on factories to ship goods also increases. However, the quality control process basically relies on manual inspection. Under high-intensity work, quality inspectors may make more mistakes or miss inspections due to visual fatigue and lack of concentration.
How to improve product yield while ensuring detection efficiency? Fujitsu decided to use AI technology to solve the problem.
Fujitsu seeks change, using AI to replace human quality inspectors
As the largest ICT supplier in Asia and the fifth largest in the world, Fujitsu's products include computers, semiconductors, middleware, etc., and it has many factories in Japan, China, the United States and other countries.
As the global manufacturing industry is promoting the trend of intelligent manufacturing, this 86-year-old company is also using cutting-edge technologies such as artificial intelligence to improve the production efficiency of its production lines.
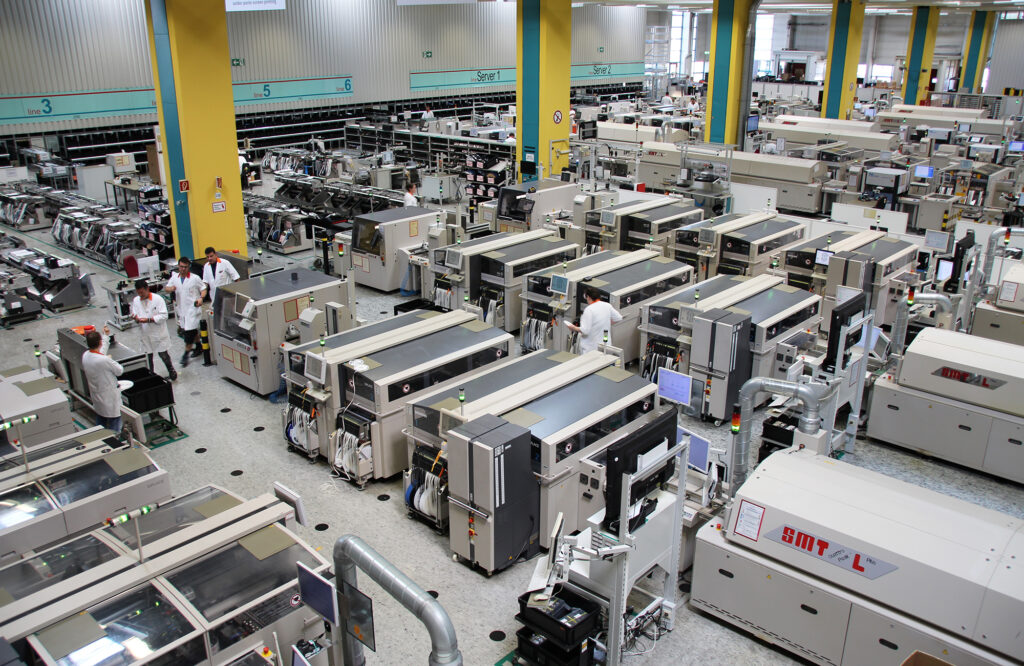
Fujitsu Laboratories announced today that it has successfully developed an AI technology for image inspection that can detect a variety of external anomalies on manufactured products, including scratches and production errors, with a high degree of accuracy.At the same time, this technology also greatly reduces the manpower and time costs of product quality inspection.
Machine vision can "find flaws" in products quickly and accurately
For a long time, product quality inspection has relied on manual visual inspection.This approach is not only inefficient, but also easily leads to problems such as missed detection, wrong detection, and inconsistent standards due to human factors.
To this end, Fujitsu decided to use machine vision instead of human eyes to detect external abnormalities of finished products. The "AI quality inspector" can determine whether a product is defective based on features such as the product's approximate shape, detailed structure, and texture.

In different types of tests, the AI Quality Inspector can also grasp the key points of the test and accurately analyze product anomalies. For example, in the shape deformation test, it will understand that the judgment of approximate shapes is the most important; while in the condition or pattern test, the AI Quality Inspector will think that the detection of texture is the most important.
also,Even if a product looks normal, if there are individual differences in elements such as coating, color, and wiring shape, AI will check these characteristics for each item and, while checking, determine whether the individual differences or abnormalities are within an acceptable range.
It is reported that the challenge of training AI to perform quality control tasks is that the model is usually trained using weighted and cumulative indices of individual features. As a result, it may be difficult to create a model that can grasp all inspection features.
In response to this, Fujitsu has developed a new AI model training method that allows AI to generate materials of various shapes, sizes and colors based on an image library of more than 5,000 artificial objects, randomly add anomalies to them, and then train the model with these anomaly images.

During the training process, Fujitsu researchers compared normal images with images restored by AI, evaluated the degree of training for each feature, such as approximate shape, detailed structure, and texture, and controlled the size, color, and number of anomalies to be added so that AI would prioritize learning features that were not captured. Afterwards, by evaluating the images restored by AI, the weak aspects of the training were strengthened.
In short, this process is equivalent to AI creating anomalies itself, then handing them over to itself for detection, and restoring the image to normal, thereby improving its skills in constant self-game.
Fujitsu verified the effectiveness of the technology during inspections at its Nagano plant in Japan.When its AI was applied to normal-looking products, the AUC score exceeded 98%, and the technology reduced printed circuit board inspection man-hours by 25%.
Fujitsu said that in the future the company will further develop related technologies and apply them to its COLMINA digital solutions to achieve digital transformation of enterprises.
From traditional to intelligent, machine vision plays a big role
In the era of Industry 4.0, artificial intelligence technology is rapidly penetrating various scenarios in the industrial field and changing our production methods.Machine vision can be said to be the "eyes" of industrial automation. Product position identification, detection, equipment operation positioning, etc. are almost inseparable from machine vision technology.
In the factory quality control system, especially in the automotive parts, 3C products, chips and other industries, product quality monitoring and defect management is a very important link, which greatly affects the quality and output speed of the product. In addition, the labor cost in this regard also accounts for a large proportion of the entire production cost.
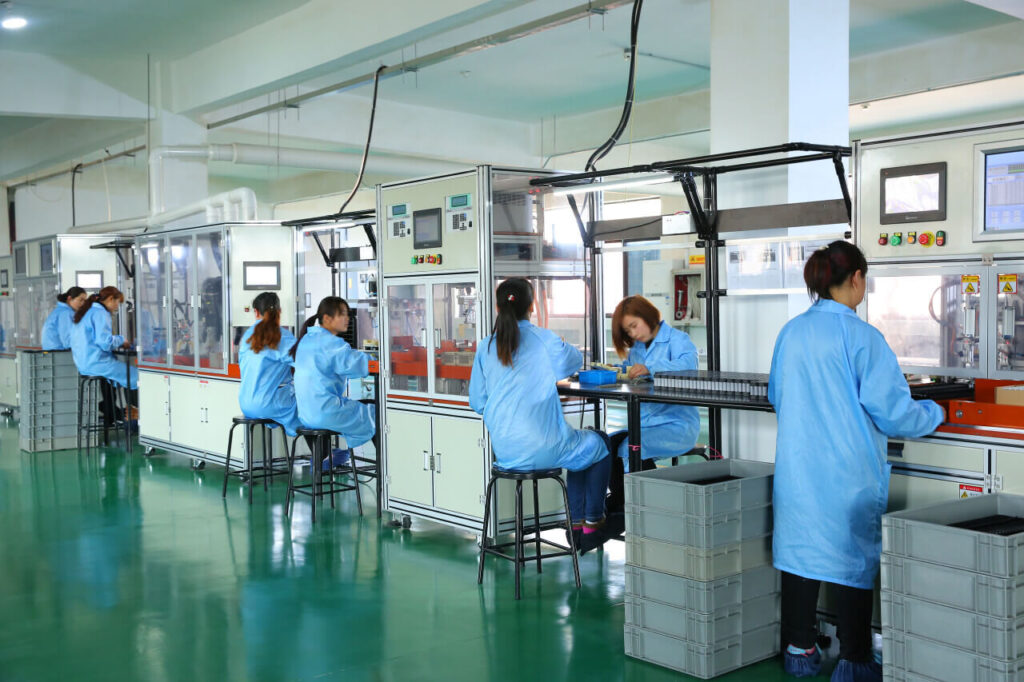
The advancement of machine vision technology has greatly promoted the automation of this link and significantly reduced missed detections and false detections.
By using machine learning algorithms and training with a small number of image samples, AI can detect tiny defects on precision products with a resolution far beyond human vision, thereby improving product yield.
Compared with human vision, machine vision has significant advantages in terms of quantization, grayscale resolution, spatial resolution and observation speed.

In recent years, many domestic and foreign companies have gradually introduced machine vision technology into production. Earlier this year, Amazon announced the launch of the machine learning service Lookout for Vision, which uses machine vision technology to provide product defect and anomaly detection services for industrial and manufacturing customers.
According to public data, in 2018, the global market size of machine vision technology used in industrial automation reached US$4.44 billion (approximately RMB 29 billion), and is expected to reach US$12.29 billion (approximately RMB 80.4 billion) in 2023, with a compound annual growth rate of 21%. The market demand is huge.
With the continuous maturity of related technologies and the continuous promotion of smart manufacturing policies, the application scenarios of machine vision technology will inevitably become more and more extensive, and the competition in this field will also be quite fierce.

News Source:
https://www.fujitsu.com/global/about/resources/news/press-releases/2021/0329-01.html