후지쯔 공장에 AI 품질 검사원 배치, 수동 검사 대비 검사 효율 25% 증가
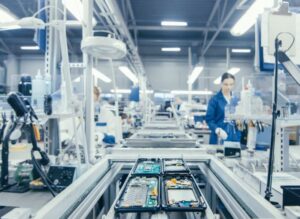
일본의 대표적인 IT 제조업체인 후지쯔는 최근 제품 외관의 이상을 감지하는 AI 기술을 개발했다고 발표했습니다. 이를 통해 인건비, 자재비 등을 절감할 수 있을 뿐만 아니라 평판 손상 및 반품/리콜 관련 비용도 절감할 수 있다고 합니다. "무인공장"이 도래했습니다.
작년 11월, Apple은 전 세계적으로 AirPods Pro를 리콜하기 시작했습니다. 그 이유는 2020년 10월 이전에 제조된 AirPods Pro는 터지는 소리나 정적인 소음을 낼 수 있으며, 시끄러운 환경, 운동 중 또는 통화 중에 이러한 소음이 커질 수 있기 때문입니다.
예상치 못하게 이 사고가 발생한 지 불과 한 달 후인 2020년 12월, Apple은 이전 iPhone 11 화면 터치 실패 문제를 타깃으로 새로운 리콜 계획을 시작했습니다.

결함 있는 제품의 반복적인 리콜은 애플의 평판을 손상시켰을 뿐만 아니라, 어느 정도 소비자의 신뢰도 잃게 만들었습니다.
따라서 제품 성능 지표 외에도 품질 관리 역시 기업에게는 매우 중요합니다.
사람들의 소비 수준이 향상됨에 따라 전자제품에 대한 수요가 늘어나고, 공장에 대한 운송 압력도 커집니다. 품질 관리 과정은 기본적으로 수동 검사에 의존합니다. 고강도 작업을 하는 경우, 품질 검사관은 시각 피로와 집중력 부족으로 인해 잘못된 검사를 더 많이 하거나 검사를 놓칠 수 있습니다.
검출 효율성을 보장하면서 제품 수율을 개선하는 방법은 무엇일까? 후지쯔는 이 문제를 해결하기 위해 AI 기술을 사용하기로 결정했습니다.
후지쯔, 인간 품질 검사원 대체 위해 AI 활용하며 변화 모색
후지쯔는 아시아 최대의 ICT 공급업체이자 세계에서 5번째로 큰 기업으로, 컴퓨터, 반도체, 미들웨어 등을 생산하는 기업입니다. 일본, 중국, 미국 등 여러 국가에 공장을 두고 있습니다.
글로벌 제조업계가 지능형 제조 추세를 촉진함에 따라, 86년 역사의 이 회사도 인공지능과 같은 첨단 기술을 활용해 생산 라인의 생산 효율성을 개선하고 있습니다.
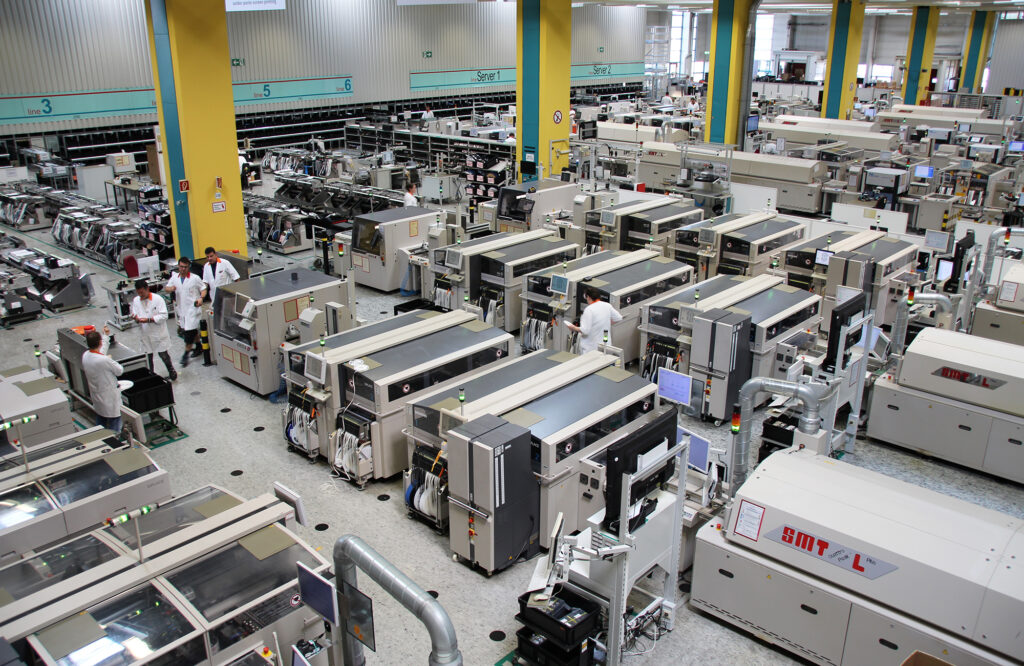
후지쯔 연구소는 오늘 제조된 제품의 긁힘, 생산 오류 등 다양한 외부적 이상을 높은 정확도로 감지할 수 있는 이미지 검사용 AI 기술을 개발하는 데 성공했다고 발표했습니다.동시에 이 기술은 제품 품질 검사에 드는 인력과 시간 비용을 크게 줄이는 효과도 있습니다.
머신 비전은 제품의 "결함을 빠르고 정확하게 찾을 수 있습니다"
오랫동안 제품 품질 검사는 수동 시각 검사에 의존해 왔습니다.이러한 접근 방식은 비효율적일 뿐만 아니라, 인적 요인으로 인해 감지 누락, 잘못된 감지, 일관되지 않은 표준 등의 문제가 쉽게 발생합니다.
이를 위해 후지쯔는 완제품의 외부적 이상을 감지하기 위해 인간의 눈 대신 기계의 시각을 사용하기로 결정했습니다. "AI 품질 검사기"는 제품의 대략적인 모양, 세부적인 구조, 질감 등의 특징을 바탕으로 제품이 결함이 있는지 여부를 판단할 수 있습니다.

다양한 유형의 테스트에서도 "AI 품질 검사관"은 검사의 핵심 포인트를 파악하고 제품 이상을 정확하게 분석할 수 있습니다. 예를 들어, 형상 변형 시험에서는 대략적인 형상을 판단하는 것이 가장 중요하다는 것을 이해하게 될 것입니다. 상태 또는 패턴 테스트 중에 "AI 품질 검사관"은 텍스처 감지가 가장 중요하다고 생각할 것입니다.
또한,제품이 정상적으로 보이더라도 코팅, 색상, 배선 모양 등의 요소에 개체 차이가 있는 경우, AI가 이러한 특성을 각 품목별로 체크하고, 체크하면서 개체 차이 또는 이상이 허용 범위 내에 있는지 여부를 판단합니다.
AI가 품질 관리 작업을 수행하도록 훈련하는 데 있어 과제는 일반적으로 개별 특성의 가중치와 누적 지수를 사용하여 모델을 훈련한다는 점이라고 합니다. 결과적으로 모든 검사 기능을 파악할 수 있는 모델을 만드는 것이 어려울 수 있습니다.
이에 대해 후지쯔는 5,000개가 넘는 인공 객체 이미지 라이브러리를 기반으로 다양한 모양, 크기, 색상의 소재를 AI가 생성하고, 이에 무작위로 이상치를 추가한 후, 이러한 이상치 이미지로 모델을 학습시키는 새로운 AI 모델 학습 방법을 개발했습니다.

후지쯔 연구진은 학습 과정에서 정상 이미지와 AI가 복원한 이미지를 비교하여 대략적인 모양, 세부적인 구조, 질감 등 각 특징에 대한 학습 정도를 평가하고, 추가되는 이상치의 크기, 색상, 개수 등을 제어하여 AI가 포착하지 못한 특징을 우선적으로 학습하도록 했습니다. 이후, AI가 복원한 이미지를 평가하고 약점을 보완하여 훈련을 강화합니다.
간단히 말해, 이 과정은 AI가 스스로 이상 현상을 만들어낸 다음, 이를 스스로 감지하도록 넘기고, 이미지를 정상으로 복원하여 끊임없는 자기 게임에서 자신의 기술을 향상시키는 것과 같습니다.
후지쯔는 일본 나가노 공장에서 검사를 통해 해당 기술의 효과를 검증했습니다.AI를 평범해 보이는 제품에 적용했을 때 AUC 점수는 98%를 넘었고, 이 기술은 인쇄 회로 기판 검사 인력을 25% 줄였습니다.
후지쯔는 앞으로 관련 기술을 더욱 발전시켜 COLMINA 디지털 솔루션에 적용해 기업의 디지털 전환을 이룰 것이라고 밝혔습니다.
전통적인 것에서 지능형으로, 머신 비전은 큰 역할을 합니다.
산업 4.0 시대에 인공지능 기술은 산업 현장의 다양한 시나리오에 빠르게 침투하여 생산 방식을 변화시키고 있습니다. 안에,머신 비전은 산업 자동화의 "눈"이라고 할 수 있습니다. 제품 위치 식별, 감지, 장비 작동 위치 지정 등은 머신 비전 기술과 거의 분리할 수 없습니다.
공장 품질관리체계, 특히 자동차부품, 3C제품, 칩 등의 산업에서 제품 품질 모니터링과 결함관리는 매우 중요한 고리로, 제품의 품질과 생산속도에 큰 영향을 미칩니다. 게다가 이 분야의 노동비도 전체 생산비용에서 큰 비중을 차지합니다.
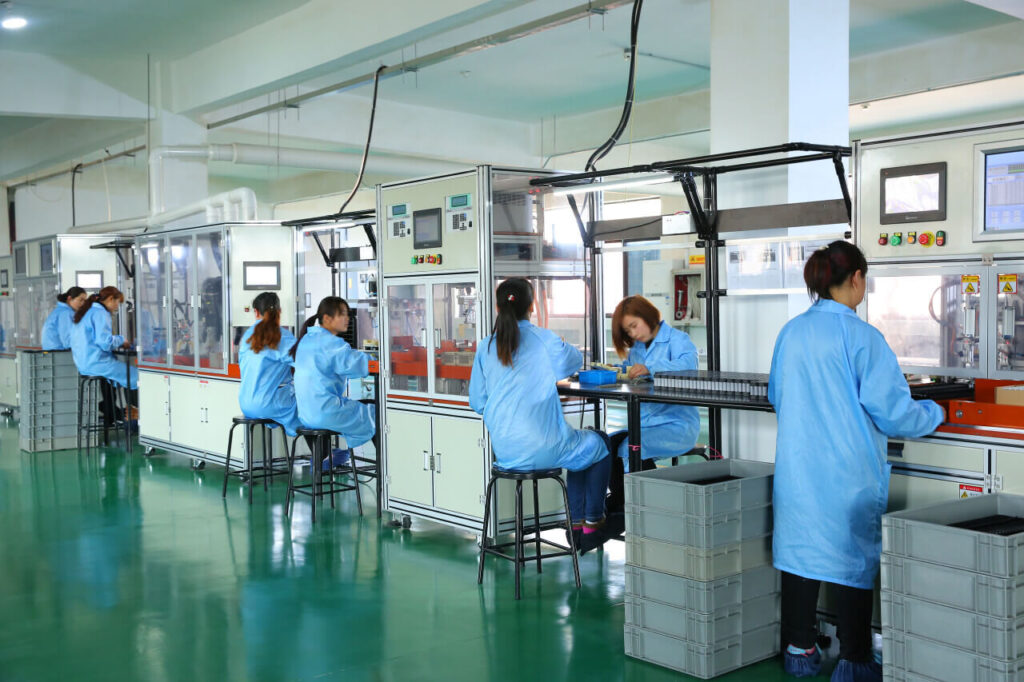
머신 비전 기술의 발전으로 이 링크의 자동화가 크게 촉진되었고, 감지 누락과 오탐지가 크게 줄었습니다.
AI는 머신 러닝 알고리즘을 활용하고 소수의 이미지 샘플로 학습시킴으로써 인간의 시각을 훨씬 뛰어넘는 해상도로 정밀 제품의 작은 결함을 감지하여 제품 수율을 향상시킬 수 있습니다.
인간의 시각과 비교했을 때, 기계 시각은 양자화, 회색조 해상도, 공간 해상도, 관찰 속도 측면에서 상당한 이점을 가지고 있습니다.

최근 들어, 국내외 많은 기업들이 점차 머신 비전 기술을 생산 공정에 도입하고 있습니다. 올해 초 Amazon은 기계 학습 서비스인 Lookout for Vision의 출시를 발표했습니다. 이 서비스는 기계 비전 기술을 사용하여 산업 및 제조 고객에게 제품 결함 및 이상 감지 서비스를 제공합니다.
공개 데이터에 따르면, 2018년 산업 자동화에 사용되는 머신 비전 기술의 글로벌 시장 규모는 44억 4천만 달러(약 290억 위안)에 달했으며, 2023년에는 122억 9천만 달러(약 804억 위안)에 도달할 것으로 예상되며, 연평균 성장률은 21%입니다. 시장 수요가 엄청납니다.
관련 기술의 지속적인 성숙과 스마트 제조 정책의 지속적인 추진에 따라 머신 비전 기술의 응용 시나리오는 필연적으로 점점 더 광범위해질 것이며, 이 분야의 경쟁도 상당히 치열해질 것입니다.

뉴스 출처:
https://www.fujitsu.com/global/about/resources/news/press-releases/2021/0329-01.html